State-of-the-art facility with advanced equipment and manufacturing capabilities. Having 10+ production lines dedicated to each customer or project allows for efficient and focused production processes.
Each line involves Melting of Aluminum, Core Making, Casting, Knock out, Chipping/Fettling, Heat treatment, Radiography testing and CNC machining, Leak Testing. This end-to-end approach allows us to maintain quality control and deliver products that meet the highest standards.
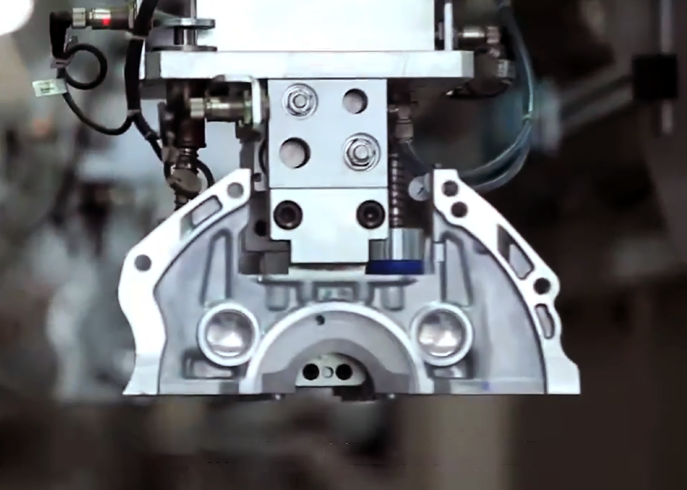
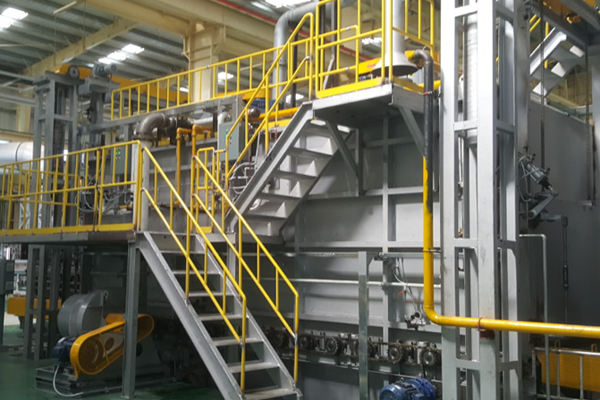
Melting
- Tower Melting cum Holding Furnace with multiple metal tapping options
- Melting Capacity per hour
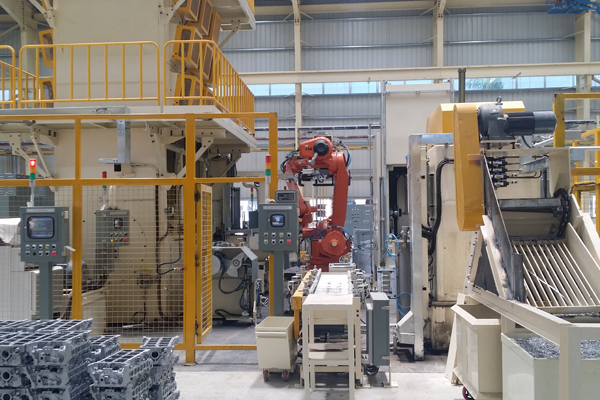
Fettling Cell
Integrated online Robotic Fettling cell
- Cooling tower
- Knockout
- Riser Cutting
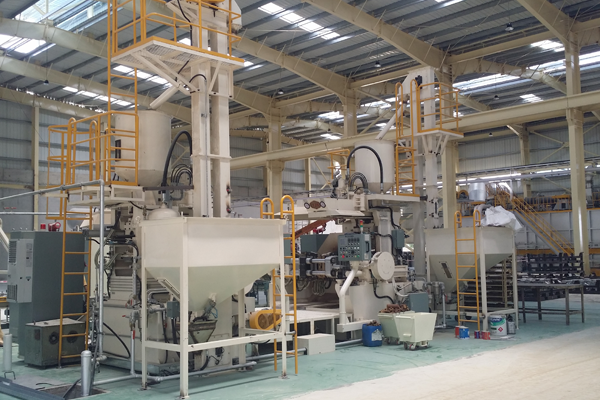
Core Making
Horizontal & Vertical Core Shooters
- Multi Cavity
- Hot box core baking technology
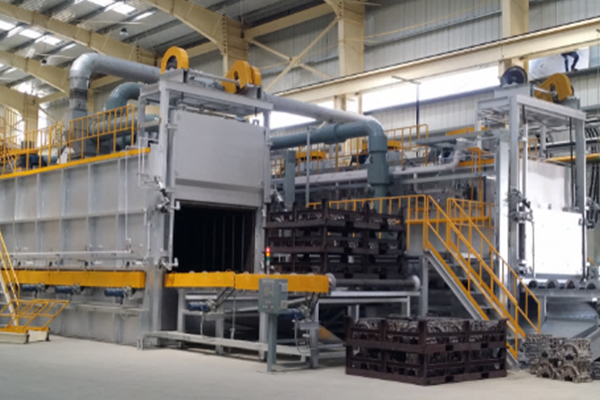
Heat Treat
Type
- Continuous High throughput Furnace
- Rotary Heat Treatment
Quenching
- Water & Air Quenching technology
- T6 & T7 Heat Treatment Process
- Certification : CQ 9.1
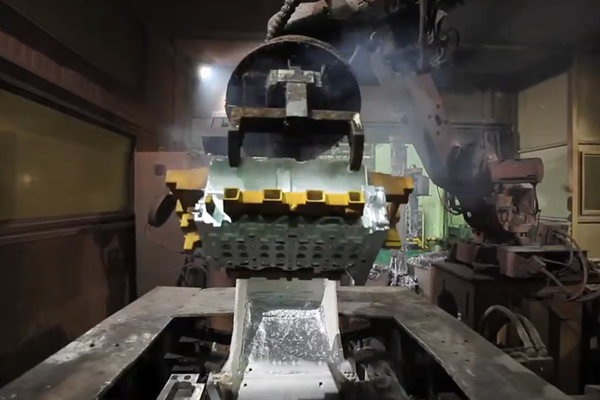
Casting
Process
- Gravity Die Casting
- Low Pressure Die Casting
- Advanced Mold Cooling system ( Air + Water)
- Integrated Robotic Pouring and Extraction system Pouring Robot interlocked with Holding furnace to prevent low temperature
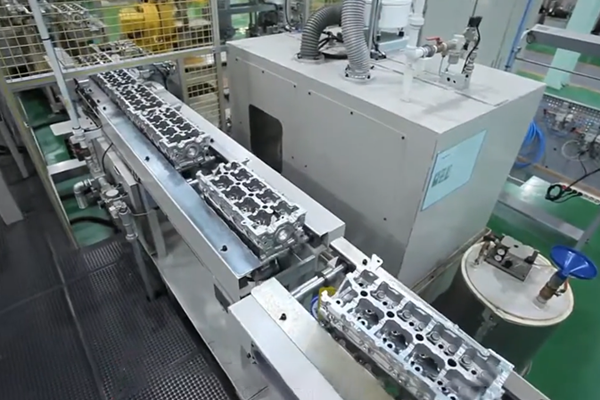
CNC Machining
- Dedicated high throughput Machining line
- Integrated 2D marking, Washing, Leak Testing of Cylinder Head
- Shrink fit liner pressing station